在汽车零部件供应商ZF公司Schweinfurt市的生产厂中有一条电动汽车驱动电机的装配生产线。把电动机的转子、定子、变速箱和电子控制器等都组装成一个整体:电动汽车驱动器。整条生产线共有30多个工位,生产启动调试阶段各工位的工作节拍为3 min。这条生产线有多个机器人单元和许多自动组装工位,有着很高的自动化程度。但也有许多人工手动的生产操作岗位,例如生产准备、内部物流以及包括设备维修保养等。在这种情况下,人与机器之间的所有过程都应该是最协调、相互配合最佳的。
为了优化装配生产线的性能,在电动汽车驱动器生产线启动调试阶段ZF公司就使用了PIA公司开发的应用软件Pia Optimum——现有机械设备性能分析工具的有力补充。
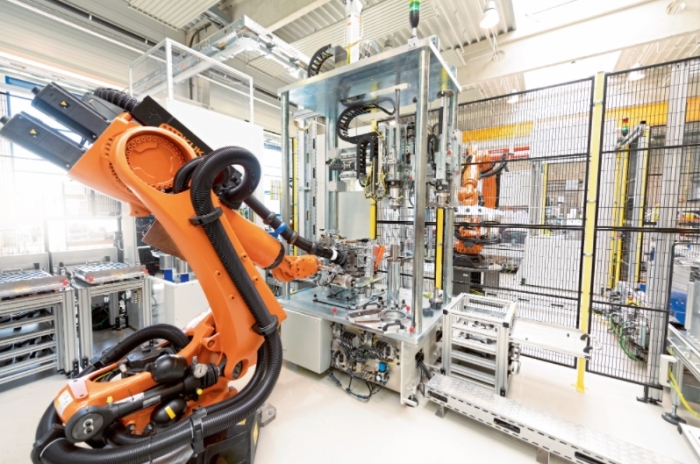
图1 在半自动化的装配线中也集成了人工手动操作的工艺流程
在生产线启动调试阶段就找出了故障隐患
评判生产设备性能优劣的关键指标始终都是设备综合效率OEE。而设备综合效率有三个组成部分:质量、可用性和效率。在机床设备的启动调试阶段上述三方面都可能存在这样或者那样的问题;而这些问题都可以用Pia Optimun进行识别、分析和评估。因此可以在很短的时间里明显提高生产设备的综合效率指数OEE,缩短设备的调整试车时间。这一应用软件主要用于发现生产线内各工位生产节拍内一些较小的、且不易被发现的工作故障隐患。Pia Optimun软件管家可以将用户的设备调整试车时间平均缩短数周之多,从而节约了大量的人力物力资源。
在生产线性能分析和优化工作期间,成立了具有奥地利PIA自动化技术公司的专家和客户公司ZF公司来自物流、设备维护保养、生产准备以及过程优化等领域的专家组成的专门工作组。奥地利PIA公司负责全球PIA 4.0工作的自动化技术专家Michael Juwan先生解释说:“Pia Optimun软件采集了生产线调试过程中最重要的数据,使其变得更加透明,也将隐含的故障源暴露的一目了然。我们按照技术标准对这些隐患进行检查分析,确定何时会出现故障、为什么出现这样的故障以及会造成什么样的损失等。”完成这些工作之后就可以轻松地确定解决问题的优先级了,并将解决问题的任务分配给合适的工作团队。这就清楚地界定问题到底是由维修保养部门负责还是由生产准备部门负责。
这种方法得出的是由各个团队按照规定的优先级展开工作,解决问题的“工作包”。“对工作包解决情况的复查也是至关重要的。复查的主要目的是核实设备调整试车时应采取的措施是否都落实到位,也可以排除因采取的新措施引发其他问题的可能性。”Juwan先生说。
将数据转换为相关信息
PIA Automation公司在开发专用设备测试软件工具方面有着多年的丰富经验,可以将装配过程中的专业数据转换为非常易懂的相关信息。这是一个自下而上的分析评估过程:Pia Optimum软件采集着所有生产过程层面的数据,并逐级简化将这些数据转换为可以显示的相关信息。通过这种方法最上层就可以知道生产线中隐含的问题,并向下分析问题的根源所在。向下分析的层次越深就越能清楚的知道问题的确切原因;最终将系统性问题、错误的装配生产工艺过程和不正确的工作站站点设置等隐患都暴露无遗。
项目开始前:供料过程不协调
在装配线项目开始之前,原生产线中某些工位之间的生产节拍不够“和谐”。在一定程度上也使装配线产生了一些废品。究其原因则非常简单:物流过程和供料过程不协调,原材料的可用性不是最佳状态。这也就使得装配工在不完全符合装配条件的情况下进行装配。后果只有一个:报废不合格的NIO组件。这也就意味着产生“缺件”和高昂的生产成本。一方面,剔除报废部件、组件必须拆卸后重新装配,比计划规定的数量少了一个;而重新装配又需要时间和零部件等资源,增加了生产成本。另一方面,不是每一个部件、组件都可以拆卸后重新装配的,例如冲压过程、压配合的生产与装配过程就是不可重复的工艺过程。在这种情况下只能将整个部组件报废,包括部组件中的一些合格品也报废了。Pia Optimum软件系统的任务就是找出错误的原因。这一软件在检查分析非常细微、非常小的错误隐患中获得了成功:它能够深入到各个装配站点工作节拍的层面进行检测分析,找出装配工作节拍中的异常和波动。

图2 Pia Optimum检查分析工具能够发现ZF公司装配线各工位中细小的问题,有助于提高整条生产线的OEE设备综合效率指数
碰撞 是产生NIO的原因之一
这里举一个Pia Optimum软件工具将工艺数据转换为质量问题信息的实例:螺栓拧紧工位出现了一定的废品率。因为拧紧工作站中的螺栓公差不符合规定的公差要求;起初估计是螺栓质量差导致的废品率。但Pia Optimun显示的信息表明:出现废品的原因并不是螺栓差,而是螺栓与部件出现碰撞造成的报废。由于碰撞致使微小的铁屑进入螺纹沟槽之中,使螺栓的拧紧变得更加困难最终导致部件报废。
根据Pia Optimum软件汇总的情况:大多数NIO不合格件都是源于碰撞。采取优化改进的技术措施之后使那些即便尺寸公差不合格的螺栓也能准确的对准螺纹底孔。这种问题很可能发生在生产线的调整试车阶段。Juwan先生说:“如果只认为螺栓公差出了问题、并不认为机床设备的设计有问题,则设备调试就不可能顺利完成。”在用了软件工具之后就可以发现如此细小的因果关系,从而将该工作站的NIO不合格品率降低到最低水平。许多小事汇聚起来就会导致一场巨大的灾难。将生产线产品移交到另一个运行良好生产系统的最后一站也往往是最重要的一站。Pia Optimum软件系统试图让所有细节变得更加清晰、更加一目了然。
同样重要的是:要支持生产线上的员工积极开展优化生产工艺流程的活动。如果一个人工手动操作过程经常出现问题,或者说操作失败,则这一操作过程可能不是人力所能胜任的。这里就需要自动化技术的帮助和支持:例如更好的拧紧螺栓,或者更方便的拾取或者定位零部件等。
经验教训:技术培训装备、装配辅助工具和物流外包
在装配线整个项目的实施过程中衍生并实施了大量规模较小的,但有着决定性意义的优化改进措施。在装配技术、过程优化、机械性能扩展、参数优化、从装配线内移出物流工位以及员工培训等综合措施作用下,稳定了装配线的工艺流程并缩短了装配时间。招聘新员工后的技术装备培训也非常有效。为此,项目团队打造了一个专门用于新员工操作培训的“学习培训单元”,重现装配线中最困难的装配过程。这就可以让新招聘来的员工在进入装配线上岗之前就能学到必须掌握的装配线操作技能。物流过程和物流责任的一致性也对提高装配线生产效率、缩短装配时间起到了积极的作用。每个人的职责和任务都再次得以明确,使每一个装配工作站的操作者都清清楚楚的知道谁要完成哪些工作与如何操作。
“在完成了第一次优化改进之后明显的提高了整条装配线的OEE设备综合效率指数。在最佳条件下设备运行时的综合效率达到了90%,这已经是一个非常令人满意的数值了,也使我们可以在这样的前提条件下进一步开始设备系统和工艺流程的第二步优化改进了。”ZF公司的制造与工程技术经理Sebastian Krause先生说道。
评论
加载更多