轻薄本、商务本、游戏本等类型的笔记本电脑已成为职场人、大学生工作、娱乐中必不可少的工具。
然而,笔记本出厂前需闯过重重 “质检难关”。一颗松动的螺丝、一处看不见的缝隙、一个断胶的屏幕,看似细微的问题,都会严重影响使用体验。在不同环节的质检过程中,3D视觉检测都发挥着关键作用。
在笔记本电脑的各个生产环节中,往往面对以下质检挑战:
海康机器人笔记本电脑3D质检方案,采用3D激光轮廓传感器,搭配自研VM3D算法平台,能够进行在线非接触式实时检测,已经广泛应用于笔记本电脑组件、主板、外壳、显示屏等全链生产环节,为企业提高检测效率和精度,实现高效率、柔性化品控管理,为产品质量保驾护航。
// 01 提高检测效率
笔记本电脑产能高,在大型生产企业中,平均不到一秒就有一台笔记本电脑下线,产品生产量大、质检环节多、效率要求高。
3D激光轮廓传感器搭配VM3D算法平台的在线测量方案,最高检测频率能达到49KHz,极大提高生产效率。
// 02 增强检测精度
人眼难以察觉精密部件或组装上的微小偏差,3D视觉测量系统可以轻松检出,大幅提高检测精度,确保每一台出厂的笔记本电脑都能达到高标准的质量要求。
在零部件及原材料准备环节中,需要准备好相关组件:如主板、显示屏、键盘、电池、外壳和内部结构件等,这些元器件通常由不同的供应商提供。
通过3D视觉检测,能快速甄别不同元器件是否存在细微瑕疵,确保其符合规格要求,大幅提升产品合格率。
在SMT贴片环节中,会在主板焊盘上涂抹锡膏,方便后续电子元件的焊接,同时使用自动贴片机将电子元器件如电容、电阻、芯片处理器等精准贴装到主板上。
使用双目单线激光轮廓传感器,通过VM3D算法平台进行面面测量、体积测量,相关算子可以对主板上焊锡的高度、体积以及桥连、拉尖等不良进行有效检测。
塑料壳体的笔记本外壳,通常通过注塑工艺加工而成,金属外壳(如铝合金)通常使用数控机床进行精密加工。加工完成后的壳体、键盘等组件,通过3D视觉进行精准检测,能够有效确保其平整度和质量的一致性。
在显示屏组装环节,需要将液晶显示面板与背光模组等进行组合,通过3D视觉,能够对胶水的位置度、宽度、高度、体积、缺陷等进行检测,有效保障密封性。
在硬件组件安装与连接环节,所有的硬件组件都会被安装到电脑内部,进行必要的连接,例如主板、硬盘与内存、电池、散热系统等。
通过3D视觉检测,能够确保安装前后状态是否符合规格要求,如检测电池仓的平整度及有无螺丝、泡棉等异物,在散热模组安装环节中检测模组的平整度、螺丝浮高等,保证组装质量。
在包装出库环节中,需要进行最后的外观检查,确保螺丝安装到位、壳体平整度符合规格,LOGO清晰完整,通过3D视觉检测能够有效检出划痕、瑕疵等缺陷。
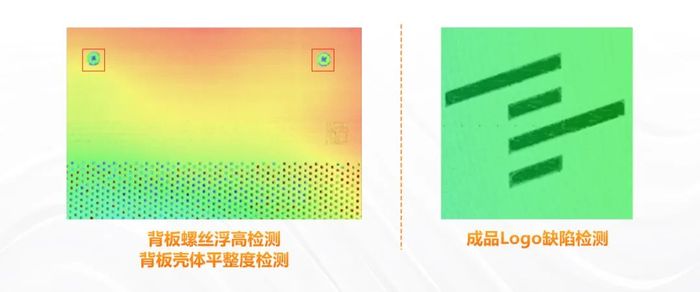
文章来源:海康机器人Hikrobot
图片来源:海康机器人Hikrobot
转载平台:微信公众号
责任编辑:朱晓裔
审 核 人:李峥
评论
加载更多